Tunipack Density Control
This is the Tunipack
Density Control
As is happening to many technological advances in the twenty-first century, the Tunipack Density Control did not have productivity as a priority (it is already very high). Instead there are other worthy goals, such as quality assurance, savings, precision, automation and efficiency.
It automatically adjusts the weight of product in each can, thus establishing the quality programmed by the machine operator.
The density control system, which enables automation of processes that used to depend on worker ability or error when placing the product, is added to all the performance features that have been implemented in Tunipack after years of canning experience across the five continents.
The entire can feed process is automatic. It no longer has to depend on human ability or error.
The Tunipack 500 DC touch screen controls the electronic adjustment of the process speed, the packing weight of each can and the final interior density of each unit.
There are several Tunipack models
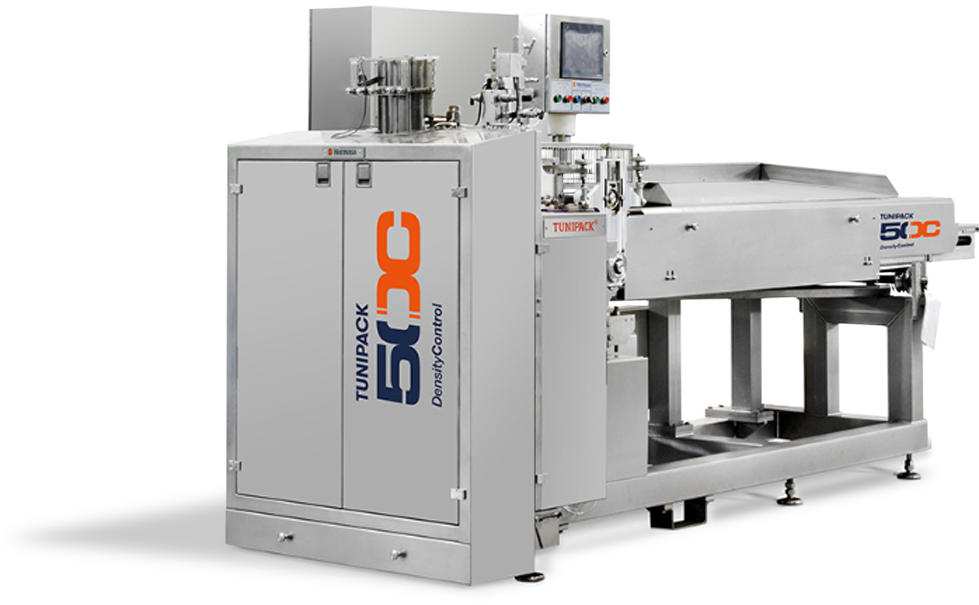
Tunipack 500DC®
Formats: cylindrical can up to a maximum 84-mm diameter (307)
Maximum and operational speeds: 500 cans/minute
- The machine is constructed entirely of stainless steel and is supplied with an EC certificate.
- High production speeds over the various ranges.
- High constant precision weight in canning using the Density Control (DC) System.
- Excellent cutting quality and final product presentation.
- High performance, independently of the method of placing the fish inside the machine and of the ability of the corresponding workers.
- Low maintenance costs
- Superlative versatility
- Programmed filling weight adjustments, without having to change formats.
- Acceptance of various can heights, without modifying the format.
- Electrical and pneumatic installations inside stainless steel conduits.
- Remote connection option via the Internet.
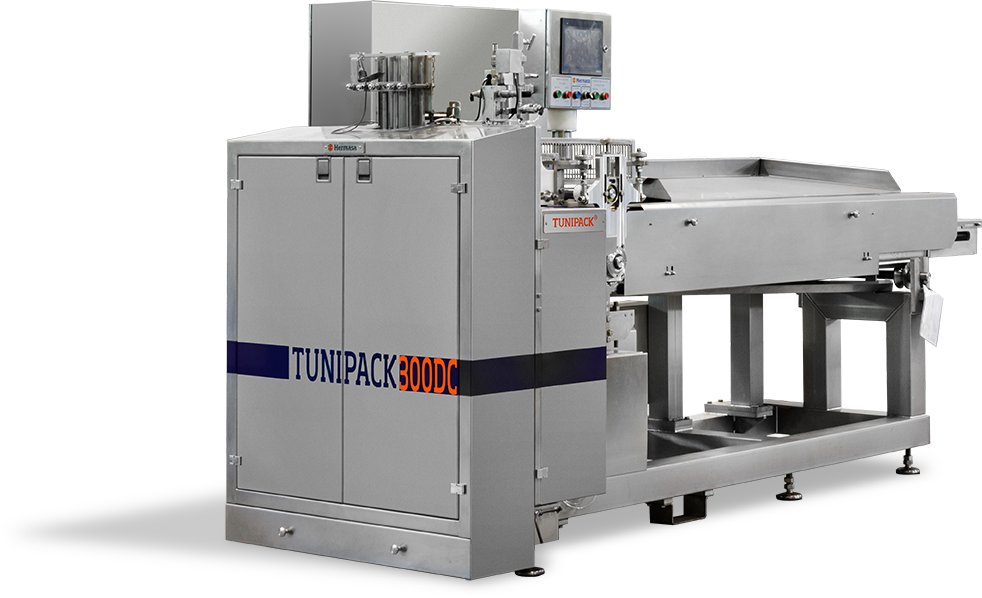
Tunipack 300DC®
- The machine is constructed entirely of stainless steel and is supplied with an EC certificate.
- High production speeds over the various ranges.
- High constant precision weight in canning using the Density Control (DC) System.
- Excellent cutting quality and final product presentation.
- High performance, independently of the method of placing the fish inside the machine and of the ability of the corresponding workers.
- Low maintenance costs
- Superlative versatility
- Programmed filling weight adjustments, without having to change formats.
- Acceptance of various can heights, without modifying the format.
- Electrical and pneumatic installations inside stainless steel conduits.
- Remote connection option via the Internet.
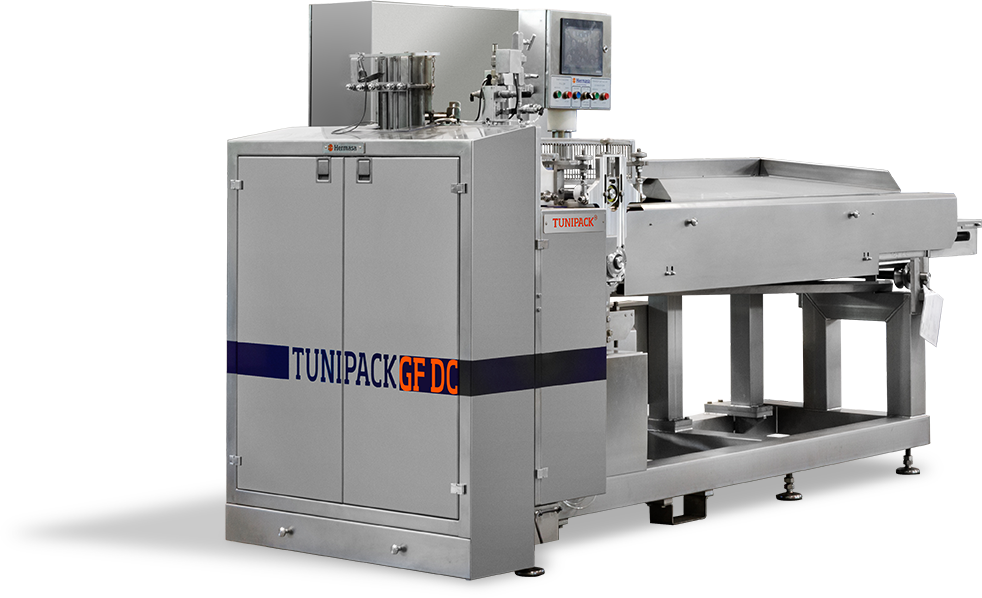
Tunipack GF DC®
Formats: cylindrical can up to a maximum 150-mm diameter (603)
Maximum speed: 60 cans/minute
Operational speed: 30 to 40 cans/minute (depending on format)
- The machine is constructed entirely of stainless steel and is supplied with an EC certificate.
- High production speeds over the various ranges.
- High constant precision weight in canning using the Density Control (DC) System.
- Excellent cutting quality and final product presentation.
- High performance, independently of the method of placing the fish inside the machine and of the ability of the corresponding workers.
- Low maintenance costs
- Superlative versatility
- Programmed filling weight adjustments, without having to change formats.
- Acceptance of various can heights, without modifying the format.
- Electrical and pneumatic installations inside stainless steel conduits.
- Remote connection option via the Internet.
¿Cómo completar la mejor línea de atún del mundo?
Each tuna process stage employs a latest-generation machine patented by Hermasa.
Research is a priority at Hermasa and this is why Tunipack only forms a part of the many types of equipment that have been leaving its Innovation Centre for decades. In fact, one of the first technological advances made by Hermasa, in conjunction with the Marine Research Institute in Vigo, was the Tunivac automatic steam cooker in the 1980s. The technicians have examined all the links that form part of the tuna canning production chain, from its arrival at the plant and classification right up to final packing. For each of these processes, Hermasa has developed the fastest and most efficient technological solution. The sum of all this advanced equipment produces extraordinary synergies when they are incorporated into the same tuna processing line.
Hermasa, el líder del sector que creó la Tunipack
The fish canning sector passed through its own industrial revolution during the latter decades of the twentieth century, just like the automotive sector had done earlier. It arrived later, but brought all the technologies and automation of the current industry. This technological transformation was caused by the demand and internationalisation of the sales made by the canning giants in the estuaries of Galicia at the beginning of the last century. Hermasa was the company that accepted the challenge to create a completely new technological sector: machines, automation and electronic devices that ended the craftsman way of life and led to the era of high industrial productivity. Nowadays, it is the world leader in this field. The same Innovation Centre where the prototypes are designed is also the machine manufacturing plant with a highly experienced workforce that includes our design engineers and the technicians that manufacture the equipment that bears our trademark.